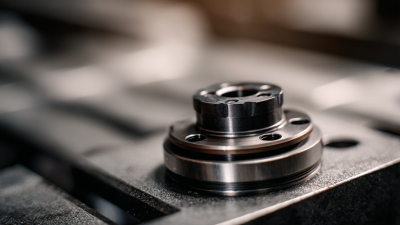
Comparative Analysis of Top Indexable Tool Repair Services for Optimal Efficiency
In the highly competitive landscape of manufacturing, the efficiency of tooling operations can significantly impact overall productivity and cost-effectiveness. Indexable tool repair has emerged as a crucial service, enabling manufacturers to extend the lifespan of their tools while maintaining optimal performance. According to a recent report by MarketsandMarkets, the global market for cutting tool repair services is projected to grow at a CAGR of 4.5%, reaching approximately $6 billion by 2025. This growth underscores the importance of effective tool maintenance strategies. As industries strive to minimize downtime and reduce operational costs, understanding the comparative advantages of various indexable tool repair services becomes essential. This blog will delve into the leading service providers, highlighting their repair methodologies, turnaround times, and overall efficiencies, offering insights that empower businesses to make informed repair service choices and enhance their manufacturing capabilities.
Read more »
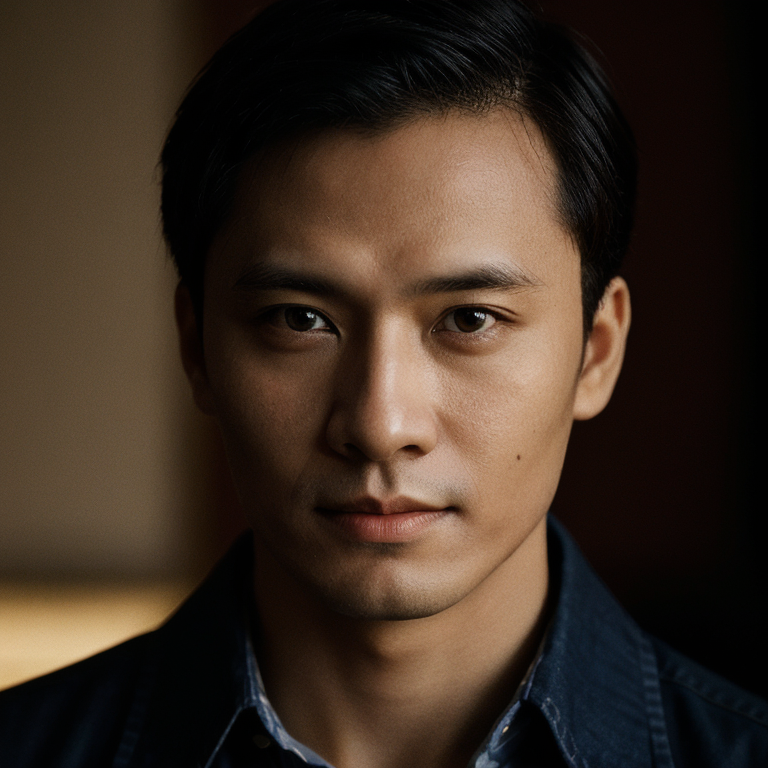
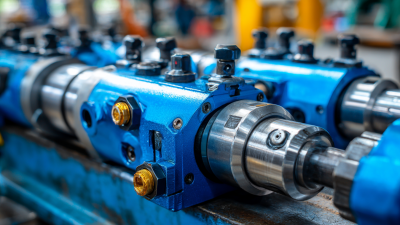
High-Quality Pneumatic Tools from China: Your Trusted Global Manufacturing Partner
In the rapidly evolving world of manufacturing, the demand for high-quality pneumatic tools has surged, making it essential for businesses to seek reliable suppliers. China has emerged as a leading global manufacturing partner, offering a diverse range of pneumatic tools designed to meet various industry needs. However, finding the right supplier can be a daunting task, given the vast number of options available. To navigate this complex landscape, companies must employ effective strategies to identify trustworthy manufacturers. This blog will explore key considerations for sourcing high-quality pneumatic tools from China, as well as top strategies for evaluating suppliers. By understanding these essential factors, businesses can ensure they partner with reputable manufacturers that deliver superior products, ultimately enhancing their operational efficiency and competitiveness in the market.
Read more »
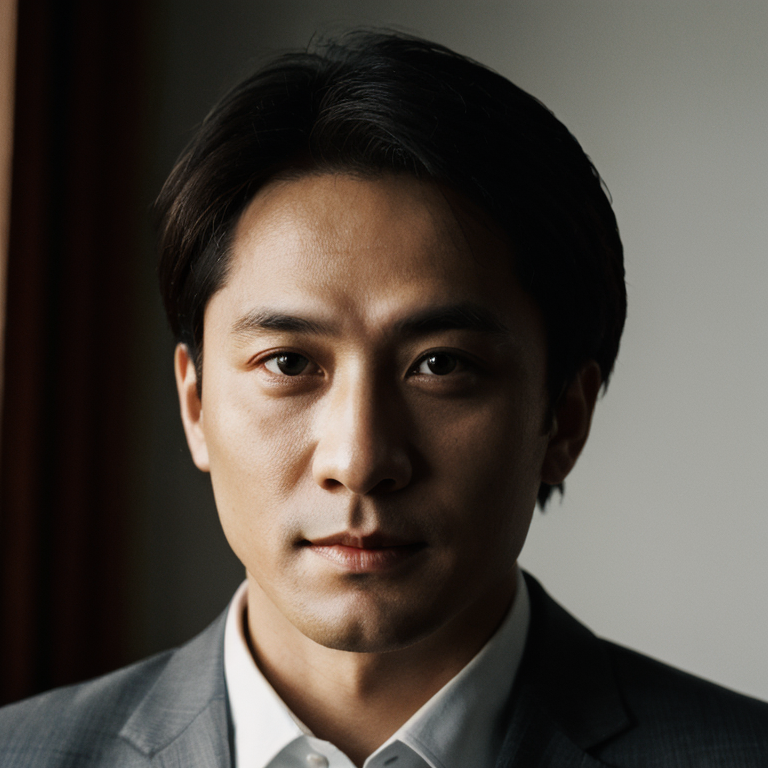
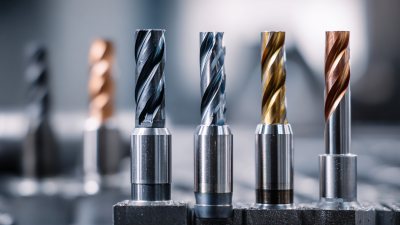
Choosing Top Quality Manufacturers for the Best Carbide Tools in Global Sourcing
In the competitive landscape of global manufacturing, the selection of top-quality manufacturers is crucial for the procurement of carbide tools, which are recognized for their superior hardness and wear resistance. According to a market report by Research and Markets, the global carbide tools market is projected to reach $20 billion by 2027, driven by the increasing demand for precision machining and manufacturing across various industries, including aerospace, automotive, and construction. As manufacturers strive for efficiency and longevity in their production processes, premium carbide tools have become an essential investment, offering not only durability but also improved operational performance. Consequently, understanding how to choose the right manufacturers for these vital tools is key to maintaining a competitive edge in today’s fast-paced market.
Read more »
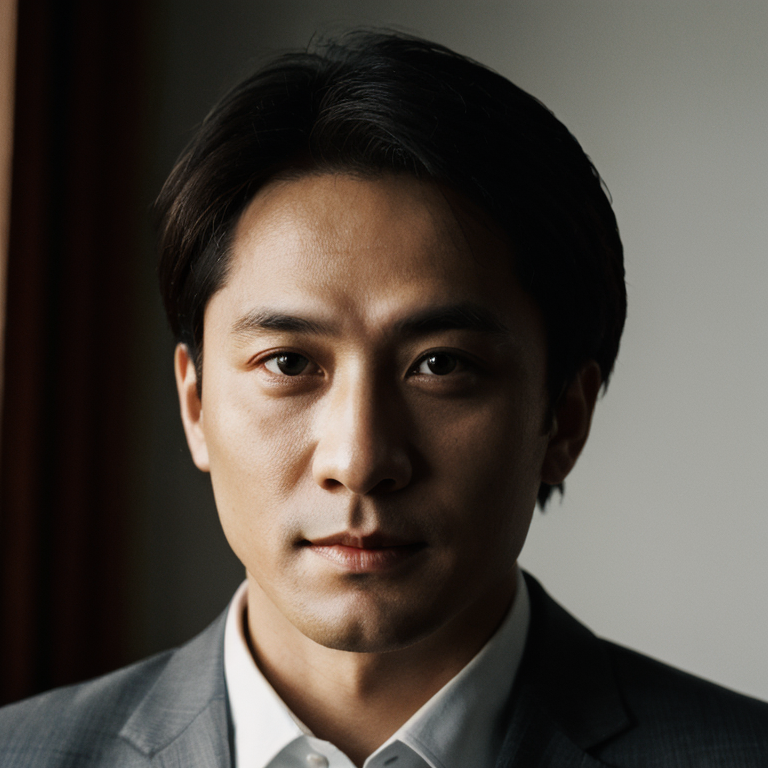
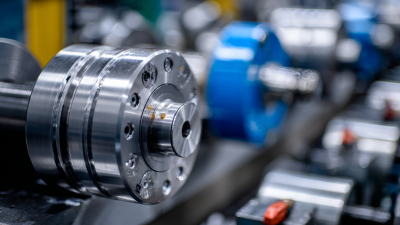
Unlocking the Future: How 2025's Tech Trends Will Revolutionize Best Tool Holders in Manufacturing
As we look ahead to 2025, the landscape of manufacturing is poised for transformation, driven by groundbreaking technological advancements that promise to reshape every aspect of production. Among these innovations, the evolution of tool holders stands out as a pivotal factor in enhancing efficiency, precision, and sustainability within the industry. Tool holders have always played a critical role in ensuring the stability and accuracy of machining processes, but emerging trends suggest that their design and functionality will undergo significant upgrades. By embracing smart technologies, automation, and advanced materials, manufacturers can unlock new levels of performance and reliability. This blog will explore the anticipated tech trends that are set to revolutionize tool holders in manufacturing, highlighting how global reliance on Chinese manufacturing will continue to uphold the promise of consistent quality while navigating the challenges of this rapidly changing industrial environment.
Read more »
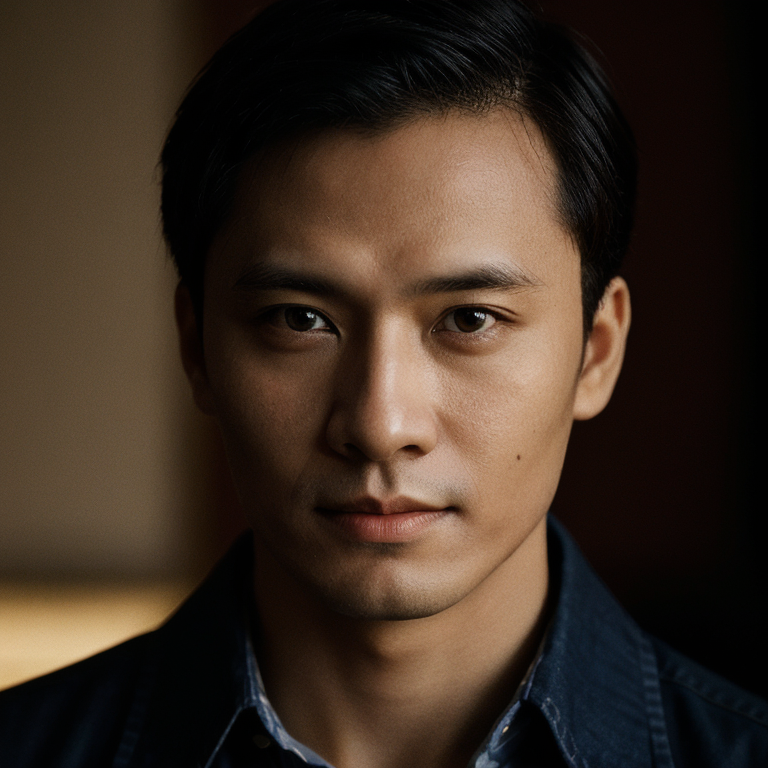
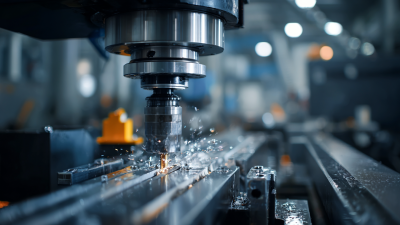
Maximizing Efficiency: The Benefits of Best Indexable Tool Repair for Your Business
In the competitive landscape of modern manufacturing, optimizing operational efficiency is crucial for business success, and one significant way to achieve this is through effective Indexable Tool Repair. According to a report by the National Tooling and Machining Association (NTMA), companies that invest in tool repair can reduce their tooling costs by up to 60%, resulting in substantial savings that can be redirected toward other value-adding activities. Furthermore, a study from the Cutting Tool Manufacturers Association (CTMA) indicates that properly maintained indexable tools can enhance productivity by 20%, showcasing the potential for improved performance and lower waste. By prioritizing indexable tool repair, businesses not only extend the lifespan of their tools but also minimize downtime and maintain a consistent quality in their production processes. This blog will explore various industry applications and present compelling reasons why investing in best indexable tool repair practices can drive efficiency and profitability in your operations.
Read more »
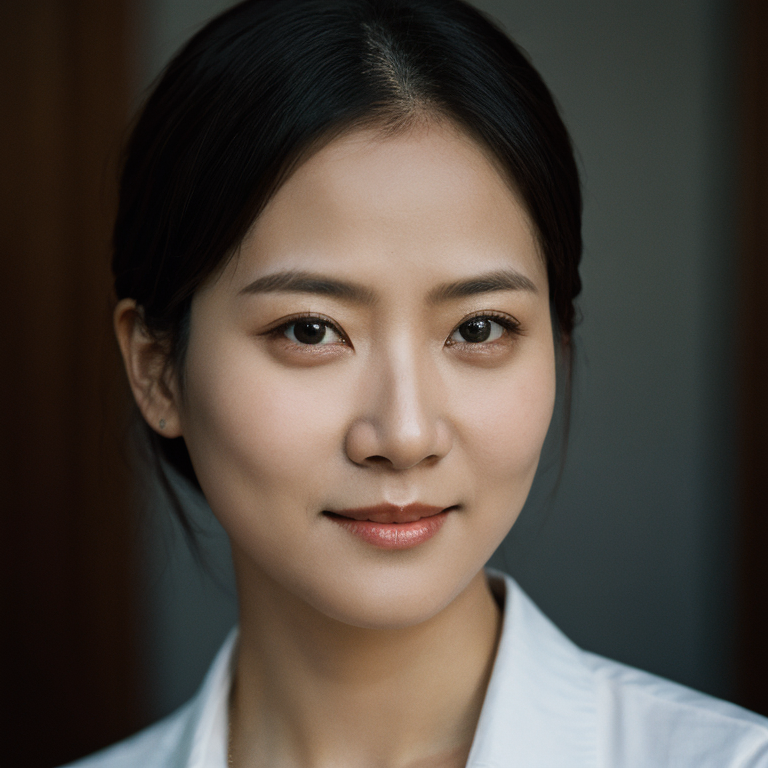
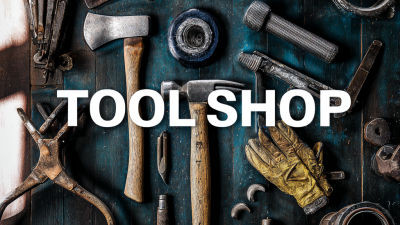
Global Buyers Discover the Excellence of Chinese Manufacturing with Best Tools Shop
In recent years, the global market has seen a significant shift towards recognizing the outstanding quality and innovation of Chinese manufacturing, particularly in the tools sector. According to a 2022 report by Mordor Intelligence, the Chinese tool industry is projected to reach a staggering USD 63 billion by 2026, reflecting a compound annual growth rate (CAGR) of 5.2% from 2021. This growth is largely driven by the increasing demand for precision tools across various sectors, including construction and automotive, where reliability and efficiency are paramount. The rise of "Tools Shop" platforms has enabled international buyers to access a wide array of high-quality tools directly from Chinese manufacturers, facilitating better prices and enhancing competitive advantage. By exploring the benefits of these specialized tools shops, global buyers can not only improve their operational efficiency but also foster strong partnerships that leverage the strengths of Chinese manufacturing excellence.
Read more »
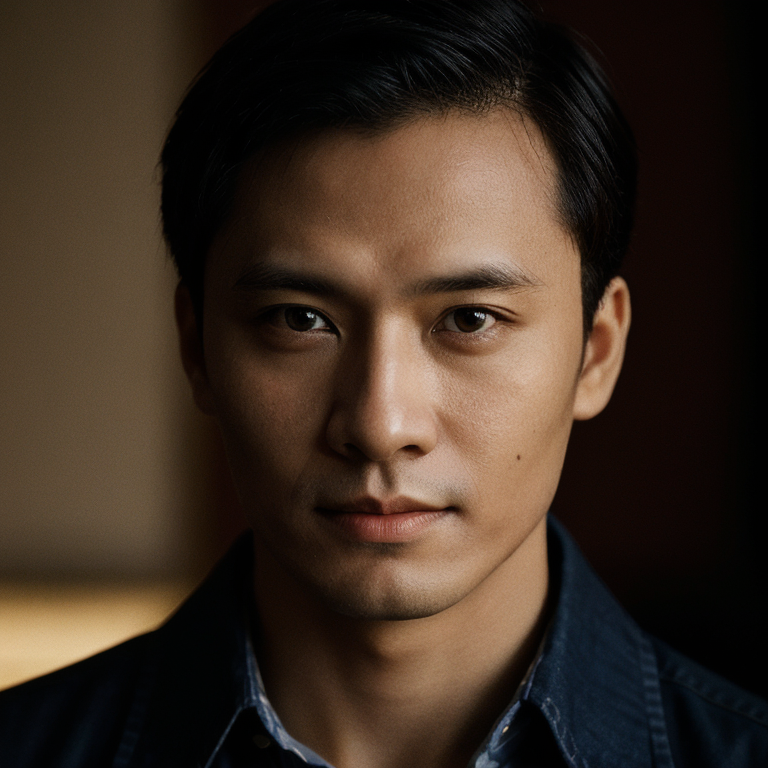
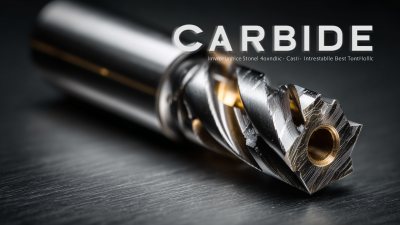
Innovative Solutions for Enhancing Efficiency with Best Custom Carbide Tooling
In today's competitive manufacturing landscape, the demand for precision and efficiency has never been higher, particularly in the realm of custom carbide tooling. Recent reports indicate that the global carbide tooling market is expected to reach approximately $15 billion by 2026, driven by a surge in automation and advanced machining techniques. The unique properties of custom carbide tooling—such as durability, high performance, and adaptability—make it an essential component for industries aiming to enhance operational efficiency. Furthermore, the incorporation of innovative solutions in tooling design can significantly reduce waste and improve production speeds, ultimately leading to cost savings and better resource management. As businesses seek to navigate the complexities of import and export certifications relevant to this industry, understanding how to effectively implement custom carbide tooling becomes crucial for achieving optimized results in manufacturing processes.
Read more »
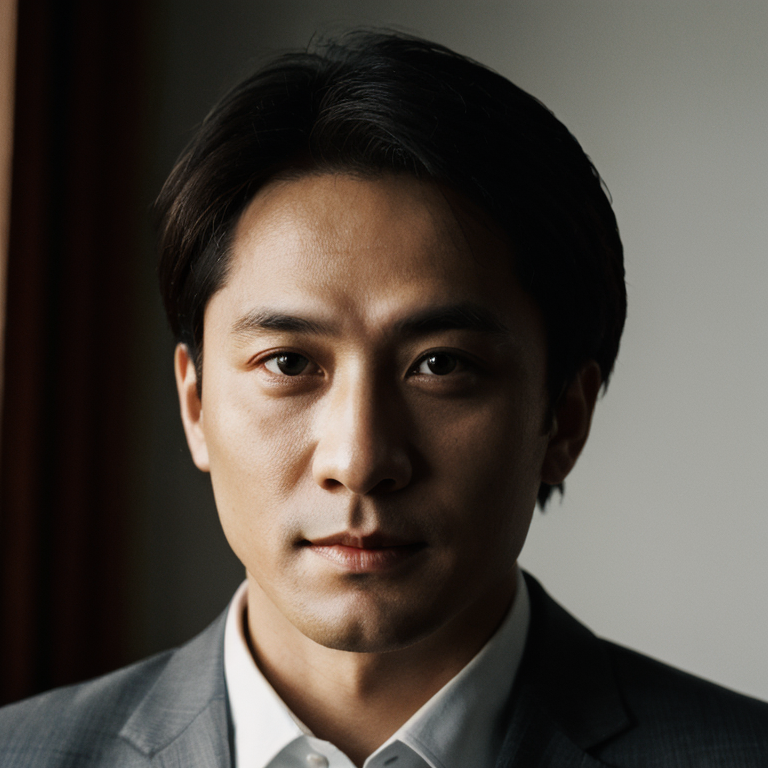
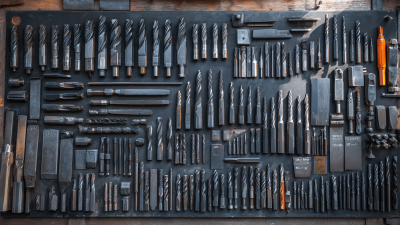
Ultimate Checklist for Sourcing the Best Carbide Tools Worldwide
In today's competitive manufacturing landscape, sourcing the best carbide tools is crucial for businesses aiming to enhance productivity and maintain quality. As industries around the world increasingly rely on high-performance materials, China's premier manufacturers have established themselves as key players in the global supply chain, exporting their cutting-edge carbide tools to various markets. This comprehensive checklist for sourcing carbide tools will guide you through the essential factors to consider, ensuring you select the right products that meet your specific needs. With a focus on quality, innovation, and reliability, understanding the landscape of carbide tool manufacturing in China can provide your business with a significant edge. Whether you're involved in metalworking, woodworking, or any other application requiring high-grade tooling solutions, this article will equip you with the insights needed to make informed decisions when sourcing carbide tools internationally.
Read more »
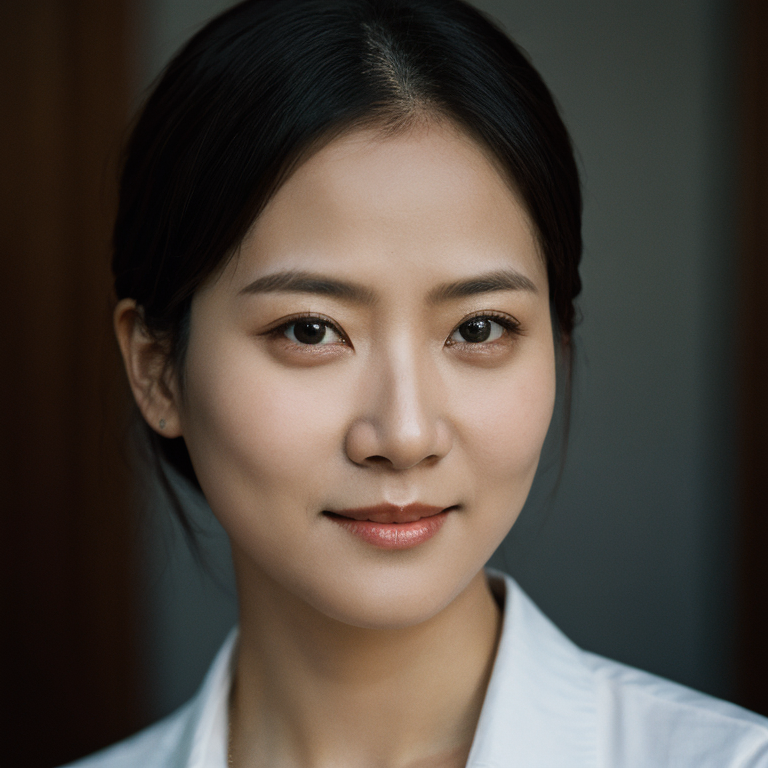
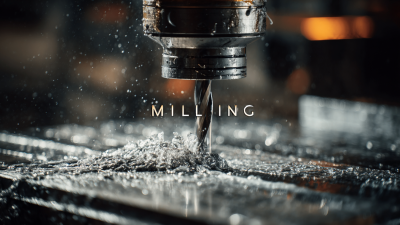
Ultimate Guide to Choosing the Best Milling Cutter for Your Manufacturing Needs
In today's highly competitive manufacturing landscape, the choice of milling cutter plays a pivotal role in optimizing production efficiency and cost-effectiveness. According to a report by Global Industry Analysts, the global market for milling cutters is projected to reach approximately $12 billion by 2026, reflecting a robust demand for precision tools in various industries such as aerospace, automotive, and metalworking. As manufacturers strive to improve their operational capabilities, understanding the advantages of after-sales service and maintenance costs associated with milling cutters is crucial. Proper selection not only influences the quality of finished products but also impacts overall production costs, with studies indicating that efficient cutter performance can reduce machining time by up to 30%. Therefore, companies must evaluate their specific manufacturing needs carefully, considering both the technical specifications of milling cutters and the associated service benefits.
Read more »
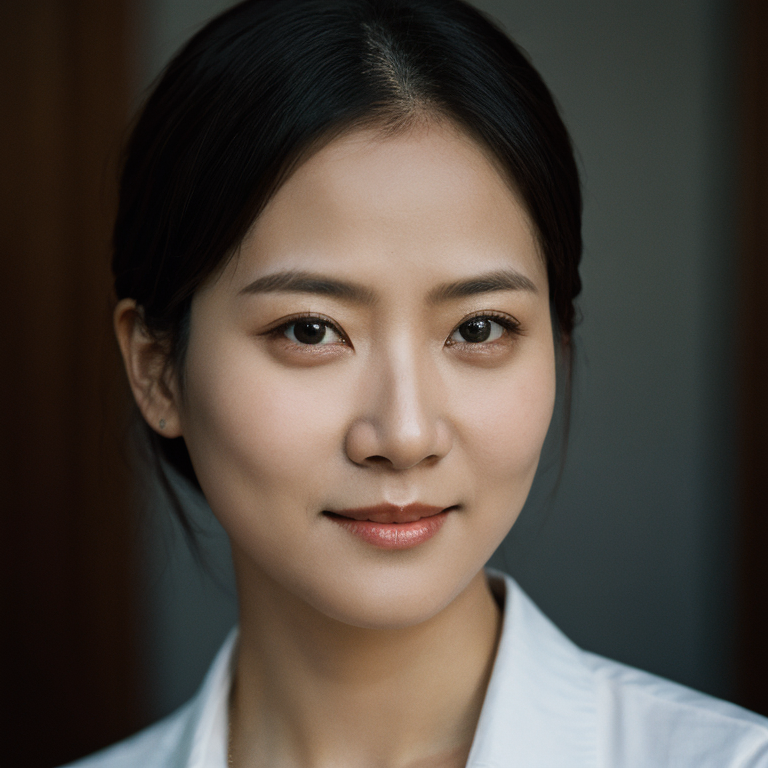
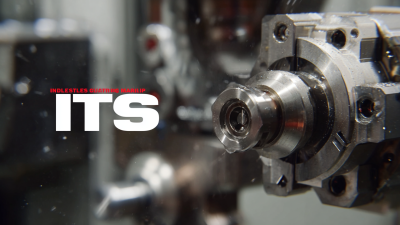
Trusted Quality Indexable Tool Repair Made in China for Global Sharing
In the ever-evolving landscape of global manufacturing, the demand for high-quality, reliable services has never been more crucial, particularly in sectors relying on precise manufacturing tools. The introduction of the Trusted Quality Indexable Tool Repair services, made in China, represents a significant advancement in this arena. With Chinese manufacturers consistently ranking among the top in global exports, they have honed their expertise in providing exceptional repair solutions that ensure the longevity and efficiency of indexable tools. This commitment to quality not only enhances the performance of tools used worldwide but also positions China as a key player in the international market for indexable tool repair. As companies increasingly seek out dependable repair options that align with their production goals, China's innovative approaches and superior craftsmanship pave the way for a new standard in tool maintenance, ready to be shared with industries around the globe.
Read more »
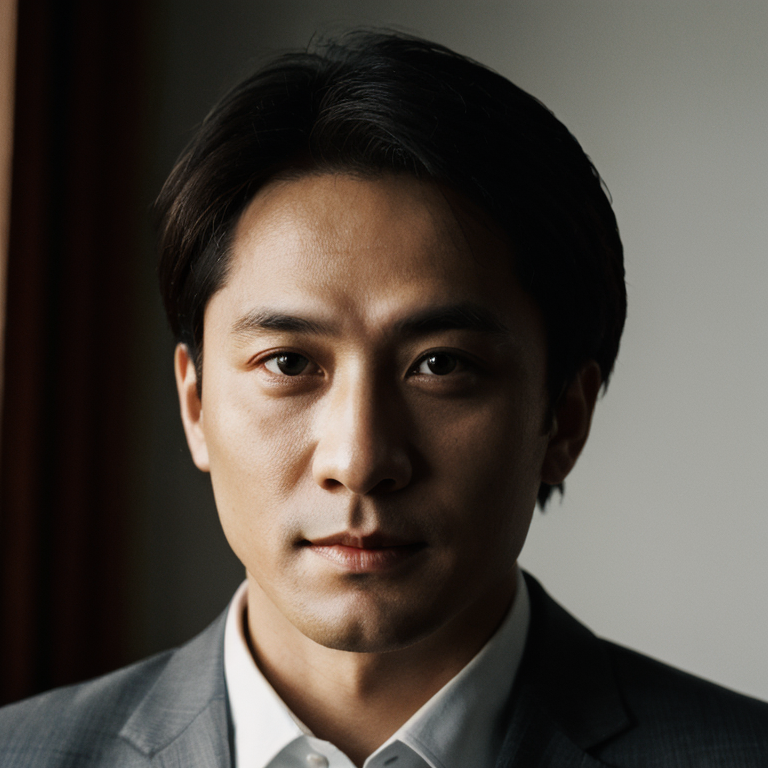
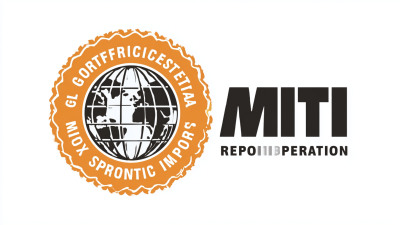
Understanding Global Certification Requirements for Best Milling Cutters Import and Export
In the ever-evolving landscape of global trade, understanding the certification requirements for milling cutters has become paramount for importers and exporters alike. According to a recent report by Market Research Future, the global milling cutter market is projected to reach over $1.2 billion by 2027, growing at a CAGR of 5.4% from 2020 to 2027. This growth underscores the importance of adhering to international quality standards and regulations to ensure product safety and performance. As companies seek to optimize their supply chains and expand their market reach, navigating the complexities of certification—ranging from ISO standards to specific national requirements—becomes crucial. In this blog, we will delve into the critical global certification requirements that shape the best practices for milling cutter import and export, equipping manufacturers and suppliers with the knowledge needed to succeed in a competitive marketplace.
Read more »
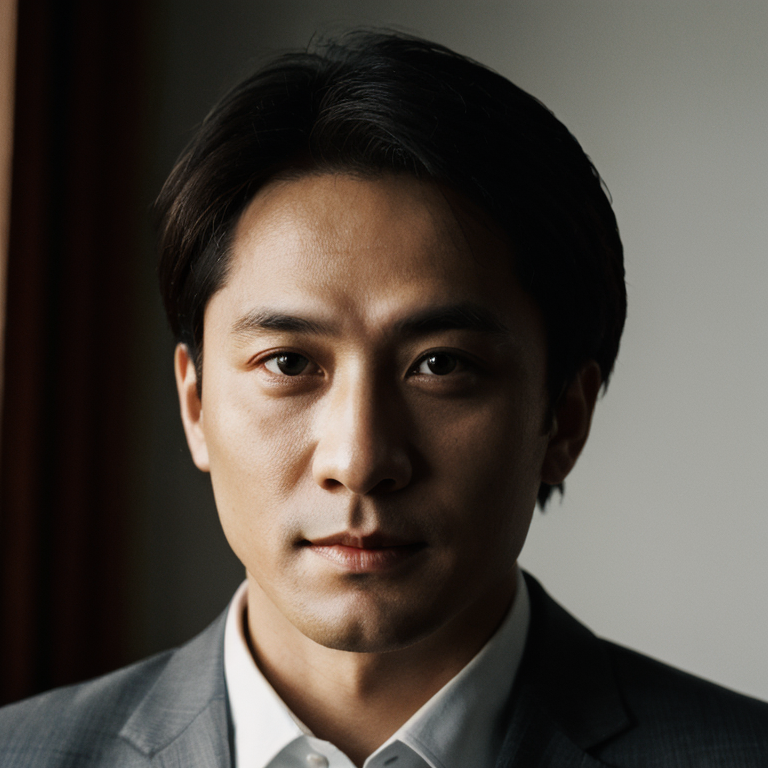
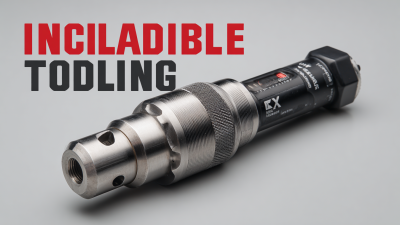
Discover the Future of Best Indexable Tooling in 2023
In the rapidly evolving landscape of manufacturing, the significance of advanced tooling solutions cannot be overstated. As we venture into 2023, the spotlight is firmly on Indexable Tooling, a game-changer designed to enhance precision and efficiency in various machining processes. This innovative approach not only underscores China's prowess in smart manufacturing but also reflects a commitment to quality that resonates globally. With a focus on performance, adaptability, and sustainability, indexable tooling is set to redefine productivity standards across industries. In this blog, we will explore the future of indexable tooling, examining key trends, technological advancements, and the vital role they play in meeting the demands of a competitive marketplace, ensuring that products are not only manufactured to perfection but are also positioned for global success.
Read more »
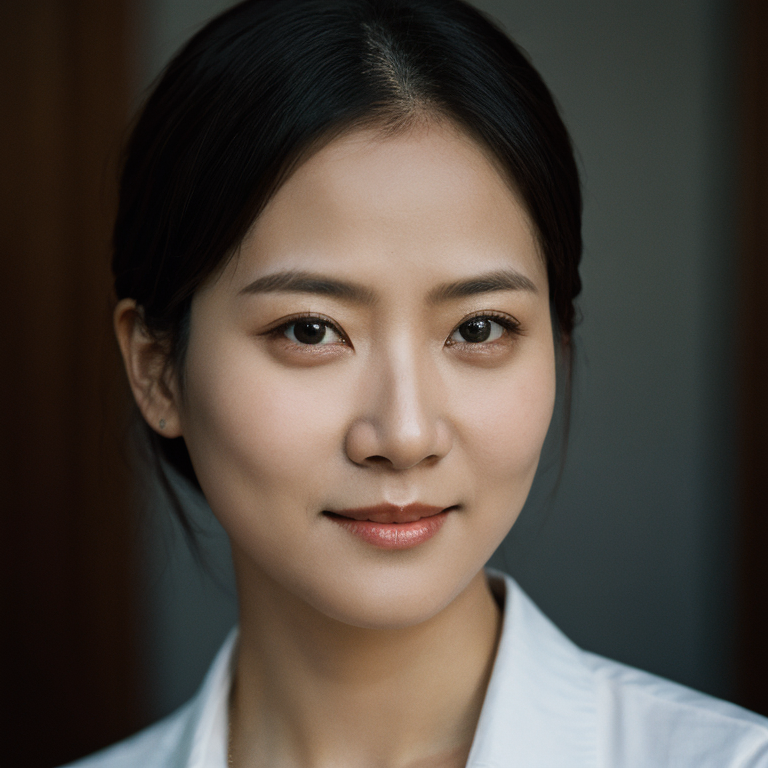
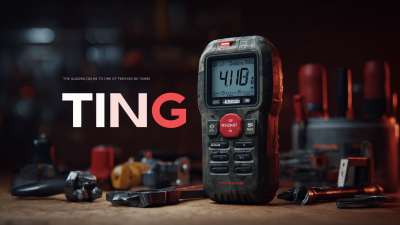
The Ultimate Guide to Choosing the Best Cutting Tools for Precision Cuts
In the realm of manufacturing and machining, the importance of selecting the right cutting tools cannot be overstated. According to a recent report by Technavio, the global cutting tools market is expected to grow by over $8 billion between 2020 and 2024, highlighting the critical role that cutting tools play in enhancing productivity and precision in various industries. The trend towards automation and advanced manufacturing techniques has further amplified the demand for high-quality cutting tools, particularly for precision cuts. As more businesses prioritize efficiency and accuracy, understanding the nuances of Cutting Tool Cutting becomes essential for engineers and machinists alike. This guide aims to provide a comprehensive overview of the factors to consider when choosing cutting tools, ensuring your operations remain competitive in an ever-evolving industrial landscape.
Read more »
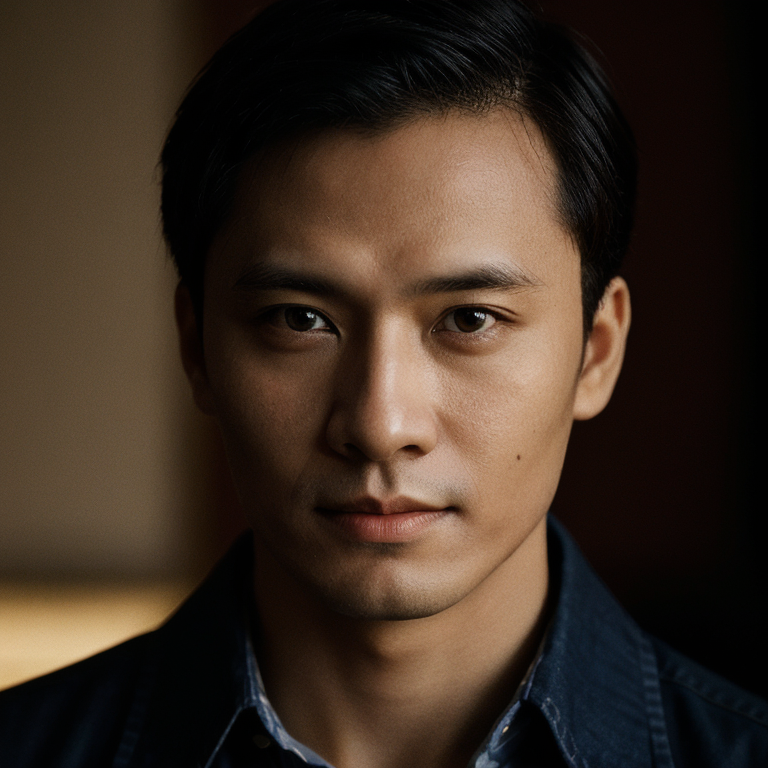
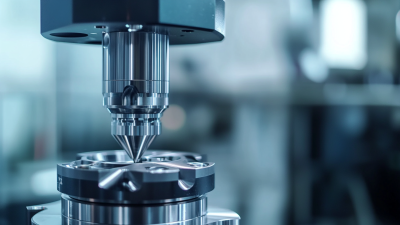
Challenges Faced in Achieving Optimal Results with Best Indexable Milling Techniques
Indexable milling has become a cornerstone in modern machining processes, offering not only precision but also flexibility in various manufacturing applications. However, achieving optimal results with indexable milling techniques is not without its challenges. According to a recent report from the Metal Cutting Industry Association, nearly 30% of manufacturers report inefficiencies in their milling processes, often attributed to suboptimal tool selection and improper cutting conditions. Additionally, a survey by the National Tooling and Machining Association indicates that 40% of respondents struggle with achieving consistent surface finishes, which can significantly impact product quality. This guide delves into the key challenges faced in the implementation of indexable milling techniques, examining factors such as tool wear, material compatibility, and the importance of effective programming and setup, all crucial for enhancing productivity and reducing costs in today's competitive landscape.
Read more »
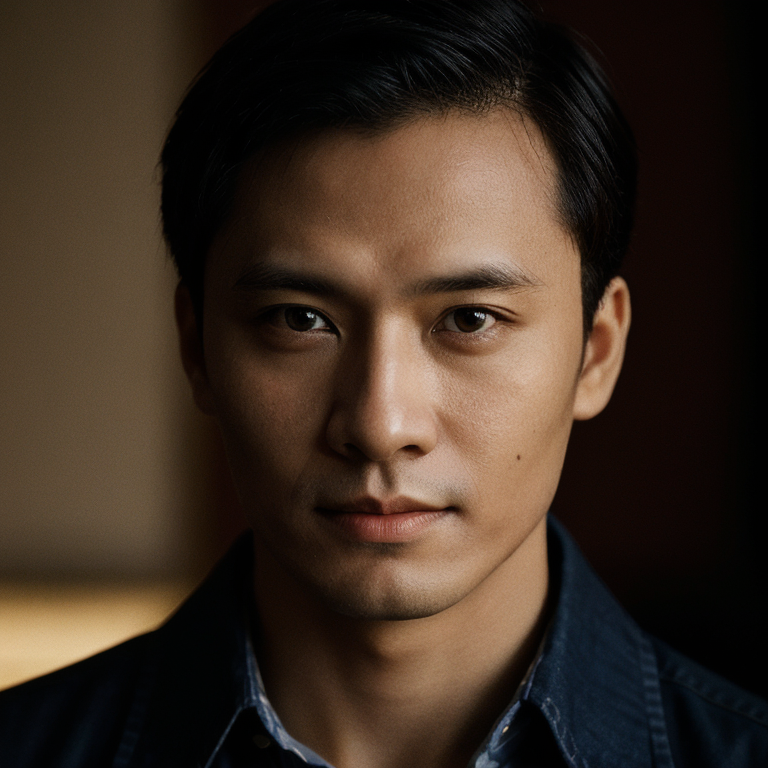
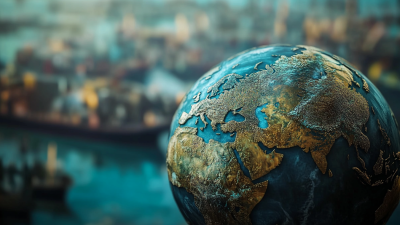
How to Navigate Global Import and Export Certifications for the Best Carbide Cutters
In the competitive landscape of manufacturing, the significance of high-quality tools, such as carbide cutters, cannot be overstated. According to a report by Allied Market Research, the global market for precision cutting tools, including carbide cutters, was valued at approximately $22.5 billion in 2020 and is projected to reach about $30 billion by 2027, growing at a CAGR of 5.6%. This growth highlights the rising demand for efficient and durable cutting tools across various industries. However, navigating the complexities of global import and export certifications poses a significant challenge for manufacturers and suppliers seeking to ensure compliance and quality. Understanding the regulatory landscape and selecting reputable manufacturers are critical steps in sourcing carbide cutters that not only meet industry standards but also provide a competitive edge in quality and performance. This blog will explore essential strategies for selecting top-tier manufacturers and effectively managing certifications in the global marketplace.
Read more »
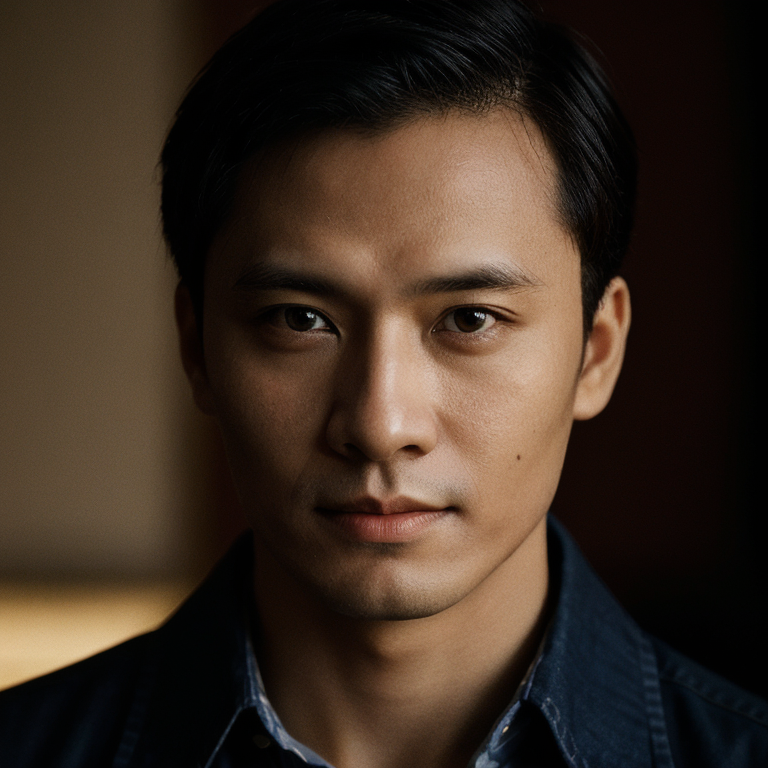