Mastering Live Tool Repair Techniques for Enhanced Machine Performance
In the competitive landscape of modern manufacturing, the performance and efficiency of machine tools are paramount for maintaining a competitive edge. According to a report by the International Federation of Robotics, the global industrial robot market is expected to exceed $41 billion by 2025, highlighting the increasing reliance on advanced machinery and technology. Live Tool Repair, a critical maintenance practice for ensuring optimal machine performance, not only extends the lifespan of equipment but also significantly reduces downtime. Recent studies indicate that organizations that prioritize timely tool repair can see up to a 30% increase in productivity, as active machine tools are central to streamlined operations and resource optimization.
As manufacturers progressively adopt more complex tooling solutions, the importance of mastering Live Tool Repair techniques becomes even more pronounced. A comprehensive understanding of these techniques not only mitigates the risk of unexpected failures but also supports a proactive maintenance approach that is crucial in today’s fast-paced production environment. The ability to swiftly and effectively repair live tools allows businesses to adapt to changing demands and maintain operational efficiency, ultimately leading to enhanced profitability. By investing in live tool repair capabilities, manufacturers can harness the full potential of their equipment, paving the way for innovation and sustained growth in an increasingly automated industry.
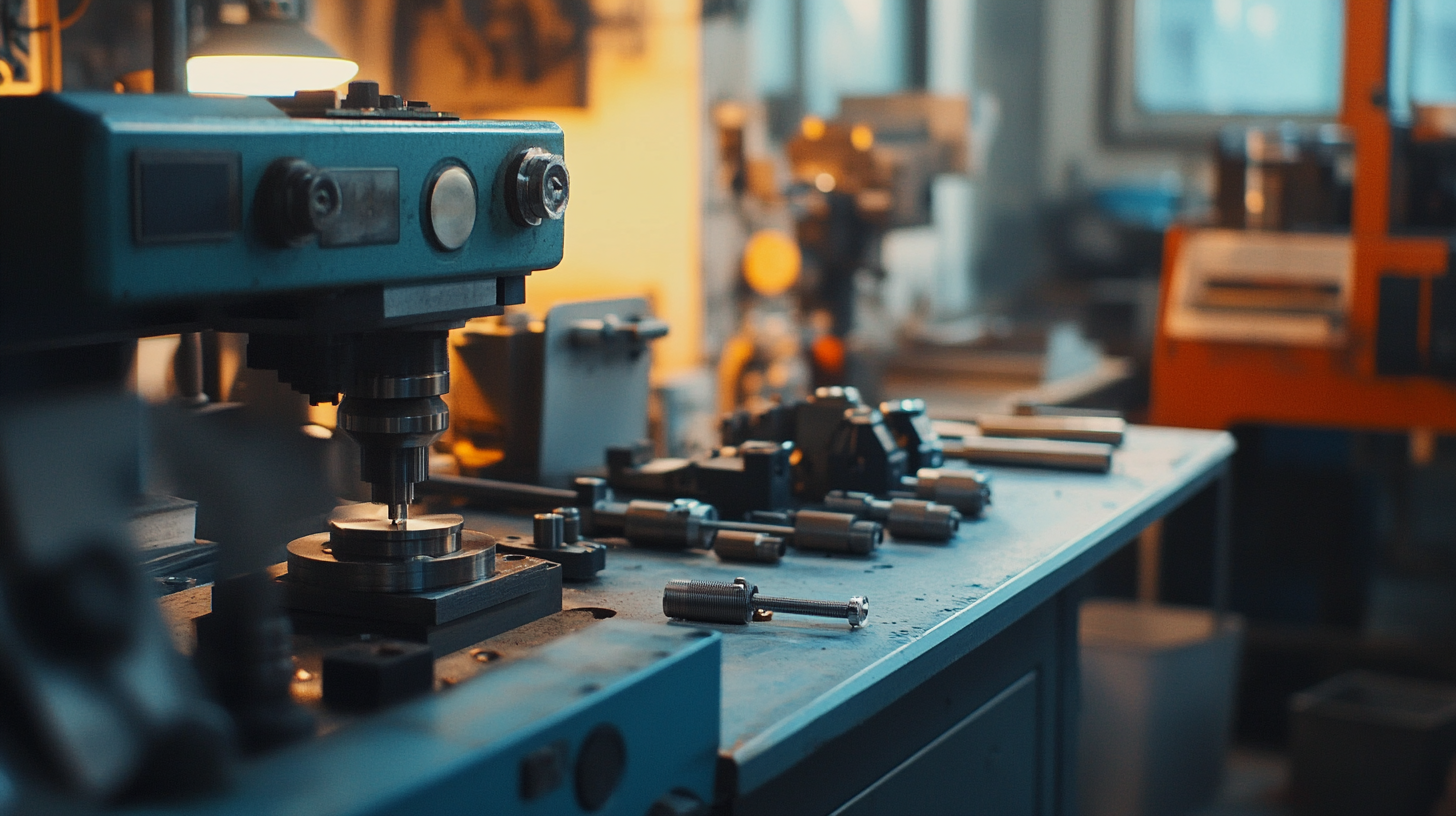
Understanding the Importance of Live Tool Repair in Modern Machinery
Live tool repair plays a crucial role in ensuring the optimal performance of modern machinery. As industries increasingly rely on automation and complex machinery, the significance of keeping live tooling in peak condition cannot be overstated. According to a recent report by MarketsandMarkets, the global CNC machine tools market is projected to reach $82.82 billion by 2026, highlighting the growing demand for efficient and reliable machinery. Live tools, which allow for simultaneous operations such as drilling and milling, are integral to maximizing productivity in machining processes. The repair of live tools not only enhances machine uptime but also significantly contributes to the longevity of the equipment. A study from the National Institute of Standards and Technology suggests that well-maintained live tools can improve part accuracy by up to 30%, which in turn reduces material waste and increases overall efficiency. Moreover, regular maintenance can mitigate costly downtime; manufacturers can save up to 15% on operational costs by implementing a proactive repair strategy rather than relying on reactive maintenance strategies. Investing in live tool repair techniques leads to improved efficiency and productivity across manufacturing operations. As technology advances, tools become more sophisticated, and the need for specialized repair methods grows. By understanding the importance of live tool repair, manufacturers can not only enhance their machine performance but also stay competitive in a rapidly evolving market.
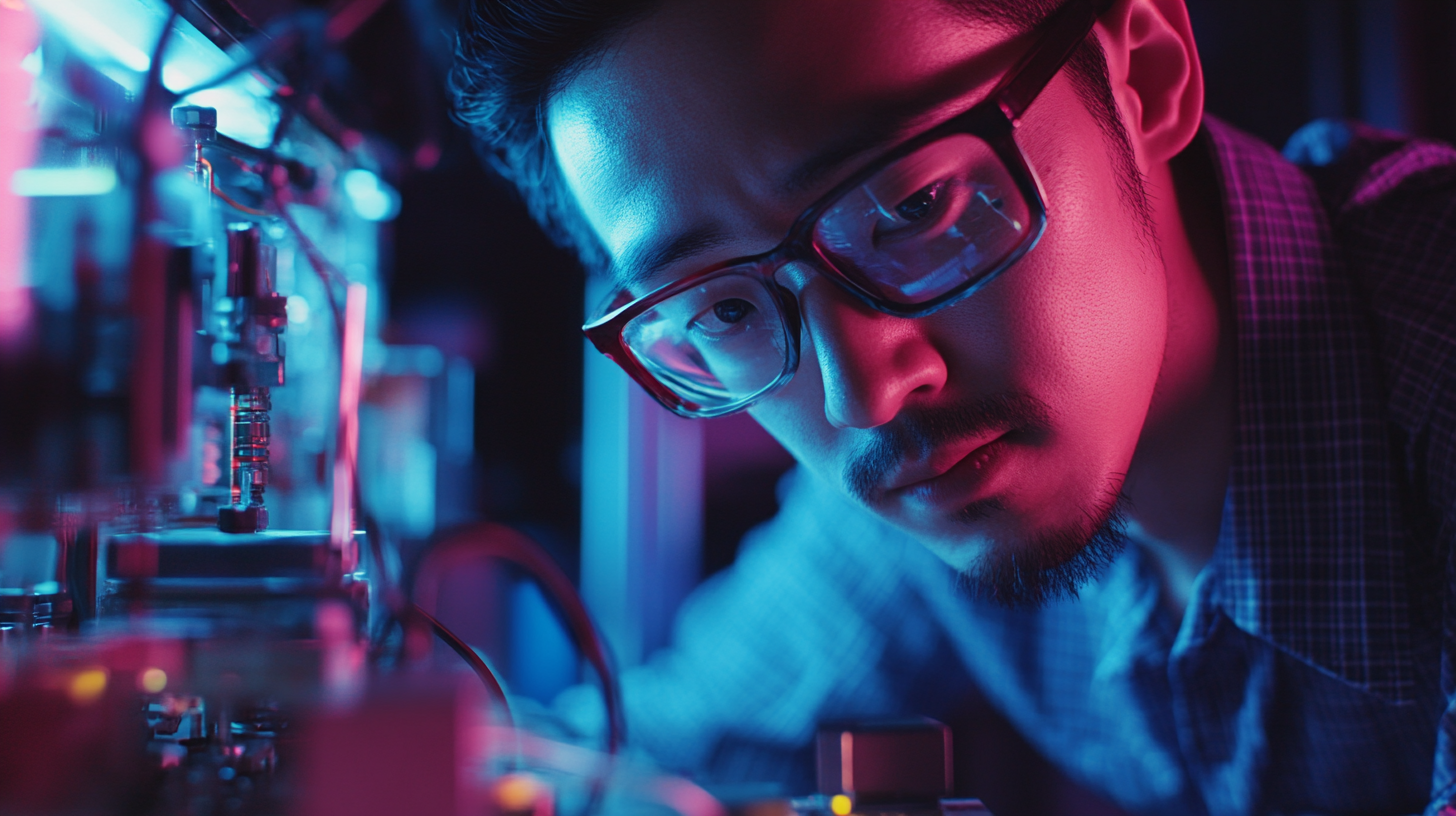
Key Components and Tools Essential for Effective Live Tool Repair
When it comes to live tool repair, understanding the key components and tools essential for effective maintenance can dramatically enhance machine performance. Live tooling has emerged as a critical feature in CNC machining, allowing for enhanced capabilities like milling and drilling during a single setup. According to a report from Grand View Research, the global CNC machine market is projected to reach $100 billion by 2025, underscoring the importance of maintaining machine integrity through proficient repair techniques.
Cornerstone components in live tool systems typically include the spindle, drive motors, and bearings, each requiring meticulous attention. The spindle, for instance, is the heart of live tooling, and any signs of wear can lead to significant downtimes and productivity loss. A study by TechSolve reveals that nearly 20% of manufacturing downtime results from machining equipment failures, highlighting the necessity of regular inspections and timely repairs. Utilizing high-precision tools such as digital calipers and micrometers can ensure that these components are within specifications.
Additionally, having the right set of tools for live tool repair is paramount. Essential tools include torque wrenches for correct fastening, vibration analysis equipment for monitoring component health, and thermal imaging cameras to detect issues before they escalate. The effectiveness of live tool systems is contingent on their upkeep; thus, investing in quality tools correlates with improved machine life expectancy and performance metrics. With the right approach to tool repair and maintenance, manufacturers can optimize their operational efficiency and minimize unplanned downtime.
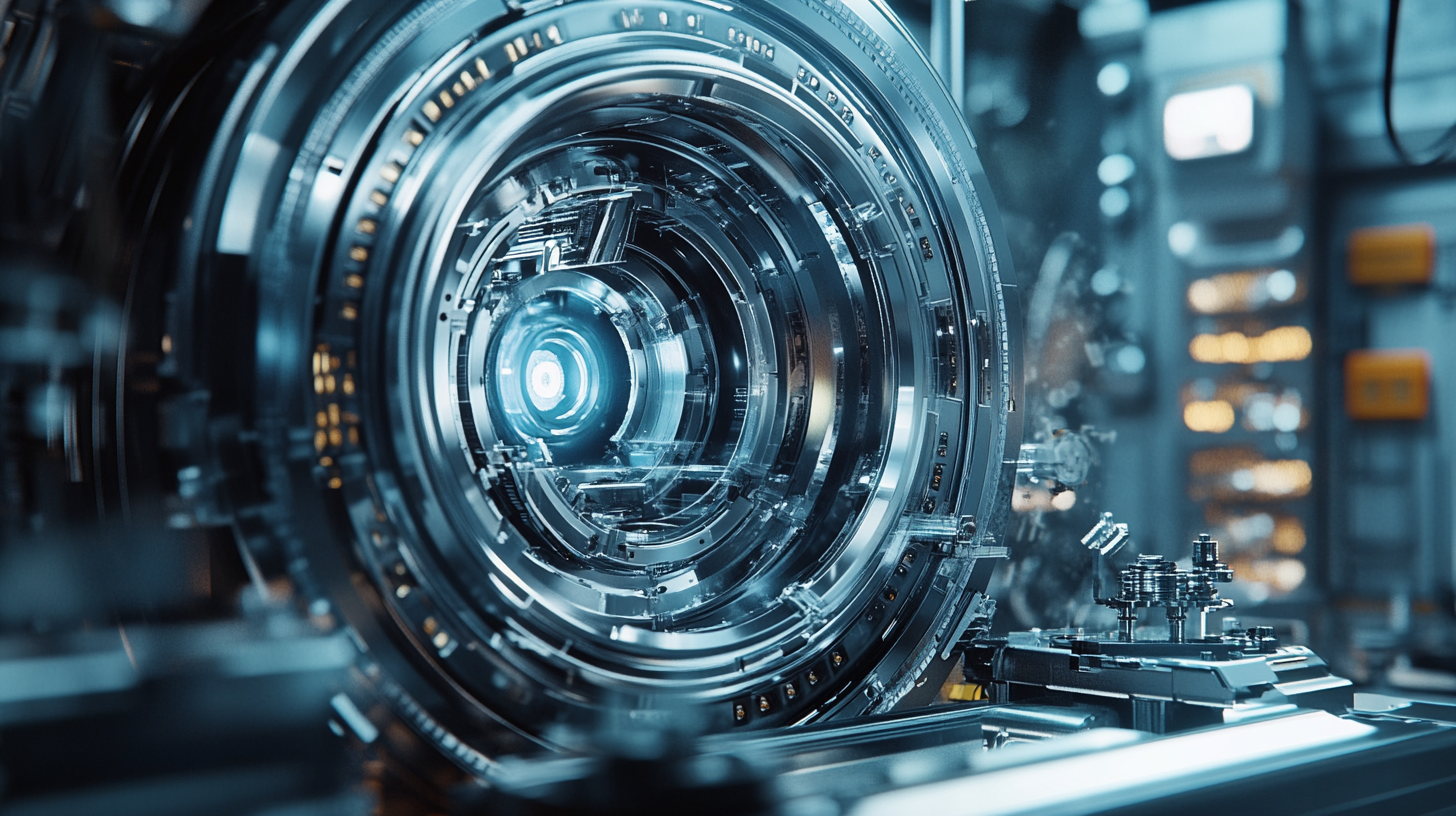
Step-by-Step Guide to Diagnosing Common Live Tool Issues
Diagnosing common live tool issues is crucial for maintaining the efficiency and longevity of machine tools. According to a report by the Association for Manufacturing Technology, up to 20% of machine downtime is attributed to tool failures and related issues. By adopting a systematic approach to diagnosing these problems, operators can significantly reduce idle time and enhance overall machine performance.
First, it's essential to conduct regular visual inspections of live tools. Look for signs of wear such as chipping or dullness in cutting edges. The 2021 Global Manufacturing Outlook revealed that tools with visible wear can lead to up to a 25% reduction in cutting efficiency. This simple inspection step can prevent more severe issues arising from continued use of worn tools, such as further machine damage or excessive vibration.
Next, operators should monitor the tool's performance metrics, particularly cutting speed and torque. A sudden deviation from established operating parameters can signify an underlying issue. For instance, data from the National Tooling and Machining Association indicates that improper torque application can lead to tool failure in as much as 30% of the cases analyzed. By closely monitoring these metrics, operators can identify potential problems early and take corrective actions before they escalate.
Lastly, ensuring proper lubrication is vital. Inadequate lubrication can lead to overheating and premature wear of live tools. Industry studies show that proper lubrication routines can extend tool life by up to 40%. Implementing a detailed lubrication schedule can prevent many common issues associated with live tools, ultimately leading to improved machine performance and reduced costs associated with repairs and replacements.
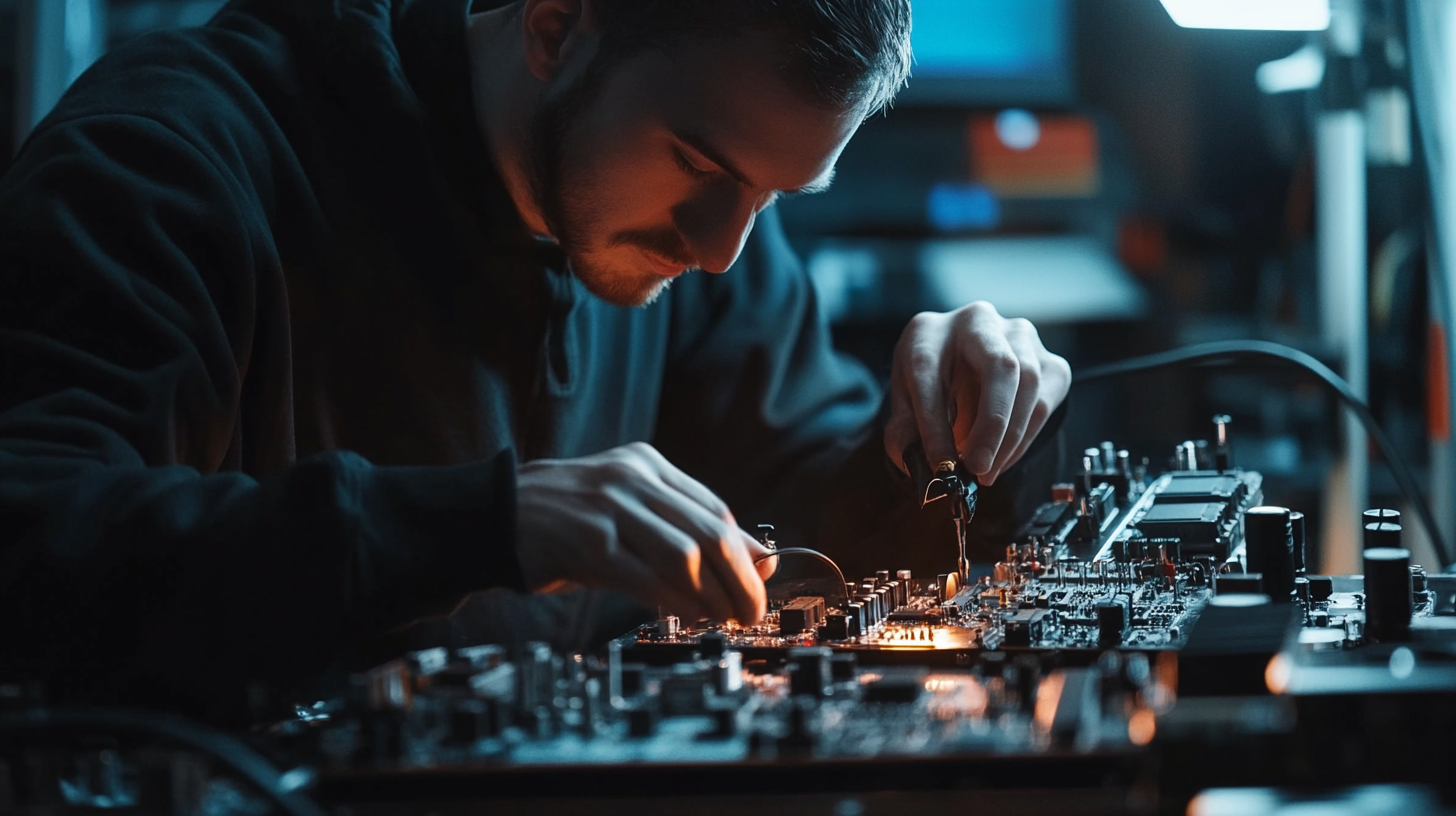
Advanced Techniques for Optimizing Live Tool Performance
When it comes to enhancing the performance of live tools in machining, employing advanced techniques is essential for optimizing both efficiency and precision. Live tools, which allow for operations such as milling and drilling while the workpiece is turning, have revolutionized CNC machining. However, to fully leverage their benefits, machinists must develop a thorough understanding of live tool repair and maintenance techniques.
One advanced technique to consider is the use of vibration analysis for diagnosing issues in live tools. By monitoring vibration patterns, operators can detect misalignments or excessive wear before they escalate into significant problems. This proactive approach not only prolongs the lifespan of the tools but also ensures that they perform at optimal levels, thereby increasing overall productivity. Regular calibration of live tools using sophisticated measurement tools can also help in maintaining their accuracy, ensuring that the tolerances of the machined parts meet the required specifications.
Additionally, incorporating advanced materials into the construction of live tools can enhance performance. Tools made from high-quality carbide or ceramic materials resist wear and heat better, leading to improved cutting performance and reduced downtime for repairs. Implementing these materials, alongside effective cooling techniques, minimizes tool degradation and maintains cutting efficiency. By focusing on these advanced repair techniques and materials, manufacturers can significantly improve the longevity and functionality of live tools, creating a more robust machining process.
Best Practices for Maintaining Live Tools for Longevity and Efficiency
Maintaining live tools in machining operations is essential for achieving longevity and optimal performance. Live tools, which integrate rotating capabilities into CNC machinery, can significantly enhance productivity when properly cared for. One of the best practices for maintaining these tools is to conduct regular inspections. Checking for wear and tear, such as dull cutting edges or excessive vibrations, allows operators to address issues before they lead to larger failures.
Another crucial aspect of live tool maintenance is proper lubrication. These tools often operate at high speeds and under significant pressure, making it imperative to use the right type and amount of lubricant. It not only minimizes friction but also dissipates heat, thus extending the lifespan of the components. Furthermore, adhering to the manufacturer's guidelines on lubrication schedules can prevent premature wear and ensure reliable operation.
Regular calibration is also vital. Live tools require precise alignment to function correctly, and even minor misalignments can lead to inefficiencies and product defects. Implementing a routine calibration schedule ensures that the live tools are always operating at optimum levels. By combining these practices—regular inspections, proper lubrication, and calibration—manufacturers can enhance the endurance and efficiency of their live tools, ultimately contributing to improved machine performance and reduced downtime.