Unlocking Precision Engineering with Tailor Made Carbide Tooling Solutions
In the contemporary landscape of manufacturing, precision engineering plays a pivotal role in enhancing productivity and ensuring superior product quality. As industries continue to evolve and embrace innovative technologies, the demand for specialized tools has surged. According to a recent report by Markets and Markets, the global carbide tooling market is projected to reach USD 18.85 billion by 2025, growing at a CAGR of 6.1%. This growth is primarily driven by the increasing need for high-performance cutting tools that can withstand extreme conditions while delivering exceptional accuracy. Custom Carbide Tooling, designed to meet specific operational requirements, has emerged as a critical solution in this arena.
The customization of carbide tooling not only improves efficiency but also significantly reduces costs associated with frequent tool replacements and downtime. In fact, a study by the American Machinist indicated that tailored tooling can enhance tool life by up to 30%, showcasing the vast potential for operational improvements. As manufacturers seek to gain a competitive edge, investing in Custom Carbide Tooling solutions becomes essential for achieving precision and consistency in production processes. By unlocking the capabilities of these specialized tools, businesses can streamline their operations and deliver high-quality products that meet the ever-increasing demands of today’s market.

The Significance of Carbide Tooling in Modern Precision Engineering
In the rapidly evolving landscape of modern precision engineering, the significance of carbide tooling cannot be overstated. As the industry navigates advancements in technology, from automation to digitalisation, carbide tools stand out as essential components that enhance performance and efficiency in manufacturing processes. With the global metal cutting tools market expected to grow significantly, reaching $141.65 billion by 2032, the demand for high-quality carbide tooling solutions is set to increase.
Turning tools, which currently hold a commanding 34.6% share of the carbide cutting tools market, exemplify the critical role of these tools in achieving precision and reliability. The projected growth of the carbide cutting tool market, anticipated to reach USD 22.2 billion by 2034, highlights the necessity for customized solutions tailored to specific engineering needs. This trend underscores the importance of investing in advanced carbide tooling to meet the ever-growing demands of sectors that prioritize accuracy and quality.
As industries continue to integrate semiconductor devices for automobiles, the connection between carbide tooling and modern engineering becomes increasingly relevant. Semiconductor technologies play a vital role in enhancing safety and connectivity in vehicles, much like how precise carbide tools contribute to the overall quality of manufactured parts. The symbiotic relationship between these technologies showcases the need for innovation in tooling solutions that not only meet current demands but also pave the way for the future of precision engineering.
Unlocking Precision Engineering with Tailor Made Carbide Tooling Solutions
This pie chart illustrates the significance of various carbide tooling applications in modern precision engineering, showing the distribution of their usage across different industries.
Key Factors Driving the Demand for Tailor-Made Tooling Solutions
In recent years, the demand for tailor-made tooling solutions in precision engineering has surged, driven by various key factors. According to a report by MarketsandMarkets, the global precision engineering market is expected to reach USD 96.50 billion by 2025, growing at a CAGR of 6.4%. This growth is fueled by the increasing need for high-quality components in sectors such as aerospace, automotive, and medical devices, where the precision of tools can significantly impact product outcomes. Tailor-made carbide tooling solutions, specifically designed to meet the unique requirements of these industries, are becoming vital to ensure efficiency and reduce manufacturing costs.
Moreover, the rise of additive manufacturing and advanced machining techniques has heightened the necessity for customized tooling. A study by Grand View Research indicates that the global machine tool market is projected to reach USD 138 billion by 2026, with a significant emphasis on bespoke solutions. Manufacturers are now more focused on enhancing their competitive edge by adopting tooling that is not only versatile but also capable of handling complex geometries and materials. Consequently, tailored tools help reduce lead times and minimize waste, aligning with the industry's push towards sustainability.
Additionally, the increasing emphasis on automation and smart manufacturing is propelling the need for specialized tooling solutions. According to the International Federation of Robotics, global sales of industrial robots are anticipated to grow to 1.7 million units annually by 2025. This trend highlights the necessity for customized carbide tools that seamlessly integrate with automated systems, ensuring precision and reliability in production processes. As industries evolve, the focus on tailor-made carbide tooling solutions will likely expand, playing a crucial role in meeting the demands of modern manufacturing environments.
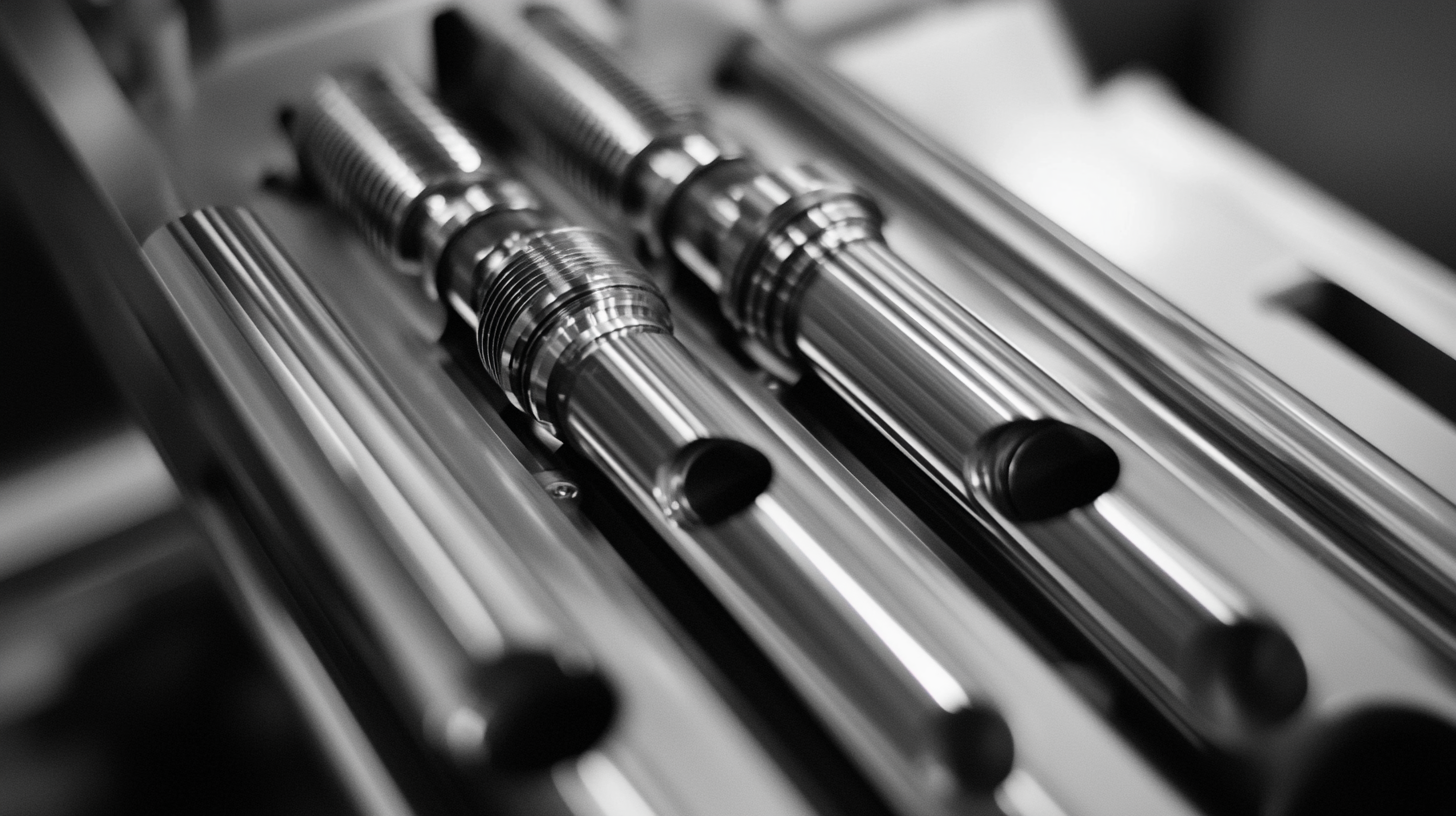
Understanding the Lifecycle Costs of Custom vs. Standard Carbide Tools
When it comes to precision engineering, the choice between custom and standard carbide tooling solutions can dramatically affect lifecycle costs. Custom carbide tools are designed specifically for certain applications, allowing for optimized performance and efficiency. This tailored approach can lead to lower operational costs over time, as these tools often provide longer tool life and reduced cycle times compared to their standard counterparts. Investing in custom tooling can, therefore, yield significant long-term savings, enhancing productivity while ensuring superior quality in the manufacturing process.
On the other hand, standard carbide tools offer a more immediate solution with lower upfront costs, making them attractive for businesses with less specialized needs or smaller production volumes. However, the trade-off may come in the form of higher replacement rates and potential inefficiencies, which can inflate overall lifecycle expenses. Understanding these dynamics is crucial for businesses aiming to strike a balance between cost and performance. As industries move toward more sustainable practices, the implications of tooling choices extend beyond just economics—custom tools can contribute to reduced waste and improved resource efficiency, aligning with broader sustainability goals.
In conclusion, careful consideration of lifecycle costs is essential in the decision-making process regarding tooling solutions. By evaluating the long-term impacts of custom versus standard carbide tools, companies can not only optimize their operational budgets but also contribute to more environmentally friendly manufacturing practices. The shift towards precision engineering with tailored tooling solutions is not just a trend; it’s a strategic move towards sustainable growth and innovation in the aerospace and manufacturing sectors.
Unlocking Precision Engineering with Tailor Made Carbide Tooling Solutions
Innovative Technologies Transforming Carbide Tool Manufacturing Processes
In the rapidly evolving world of precision engineering, innovative technologies are playing a pivotal role in transforming carbide tool manufacturing processes. According to a report by Grand View Research, the global carbide tools market was valued at approximately $18.3 billion in 2021, and it is expected to exhibit a compounded annual growth rate (CAGR) of 4.5% from 2022 to 2030. This growth is driven by the increasing demand for high-performance tools that can withstand intense operational conditions, thereby offering manufacturers a competitive edge.
One significant advancement is the integration of additive manufacturing techniques in carbide tooling. By utilizing 3D printing technologies, manufacturers can produce complex geometries that were previously unattainable through conventional methods. This not only reduces material waste but also minimizes lead times, allowing for more agile production cycles. Additionally, processes such as powder metallurgy have enhanced the properties of carbide tools, resulting in improved hardness and wear resistance, as highlighted in the latest studies published in the Journal of Cleaner Production.
Moreover, the incorporation of advanced coatings and surface treatments has revolutionized the durability and efficiency of carbide tools. Reports from market analysts indicate that tools with specialized coatings can extend tool life by up to 300% compared to untreated alternatives. These innovations not only enhance performance but also contribute to sustainability efforts by reducing the frequency of tool replacements, ultimately leading to a decrease in resource consumption and waste generation in the manufacturing sector. As precision engineering continues to embrace these cutting-edge technologies, the landscape of carbide tooling solutions is set to become even more sophisticated and specialized.
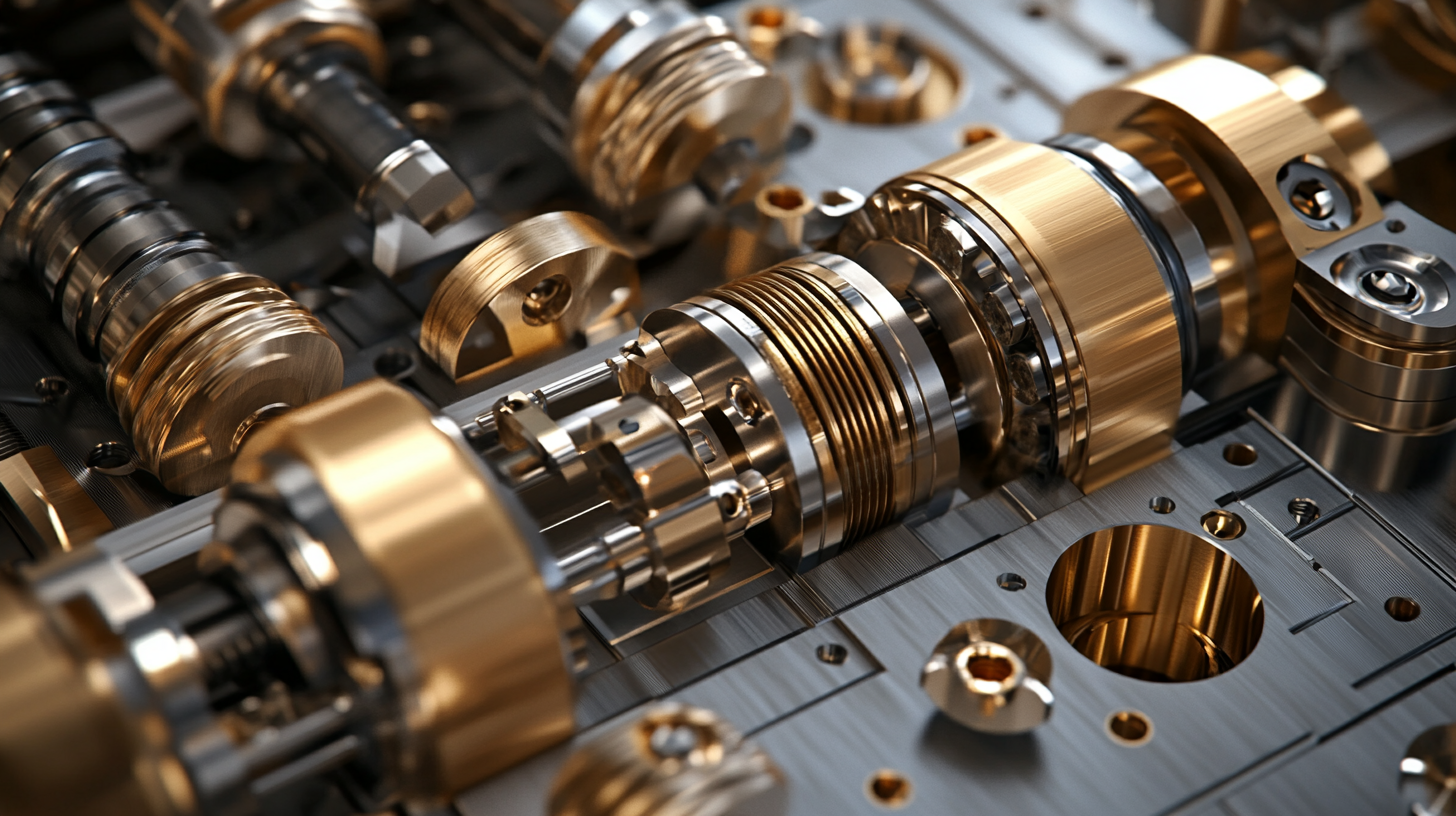
Case Studies: Achieving Operational Excellence with Customized Tooling Solutions
In the landscape of precision engineering, the demand for tailored carbide tooling solutions is increasingly evident. Recent case studies highlight how customized tooling not only enhances operational efficiency but also contributes significantly to achieving excellence across various manufacturing sectors. By leveraging specialized tooling that is designed to meet the unique requirements of each operation, companies can improve their production rates and reduce waste.
As industries embrace digital transformation, the focus on integrated solutions like Customer Relationship Management (CRM) systems parallels the necessity for specialized tools in manufacturing. Just as CRM systems are pivotal for optimizing customer interactions and driving business growth, bespoke carbide tooling solutions streamline production processes, leading to enhanced quality and performance. The synergy between cutting-edge technology and precision engineering fosters a competitive edge, enabling organizations to adapt swiftly to market demands.
Furthermore, case studies reveal that businesses utilizing tailor-made carbide tooling experience significant gains in their operational workflows. By analyzing their specific needs and challenges, companies can implement solutions that not only fit their production criteria but also align with their strategic goals. This tailored approach exemplifies how innovation and customization can play a crucial role in achieving operational excellence in precision engineering.
Unlocking Precision Engineering with Tailor Made Carbide Tooling Solutions
Case Study | Industry | Challenge | Solution | Results |
---|---|---|---|---|
Aerospace Components | Aerospace | High precision requirements with tight tolerances | Customized carbide tooling designed for specific part geometries | Improved accuracy and reduced waste by 30% |
Automotive Engine Parts | Automotive | Inconsistent tool life and performance | Tailor-made carbide tools with advanced coatings | Extended tool life by 50% and consistent performance |
Medical Device Manufacturing | Medical | Strict regulations and quality standards | Customized tooling solutions ensuring compliance | Achieved 100% quality compliance and reduced cycle time |
Aviation Parts Production | Aviation | High variability in part designs | Adaptable tooling system to accommodate design changes | Reduced lead time by 40% and enhanced flexibility |
Related Video
-
Manufacturing of a special diameter 2 flute solid carbide end mill
View: 345Channel: Spectra Carbide Tooling Technology -
Incredible Machining: Parts Made In Seconds Using 8 Spindles
View: 593979Channel: TITANS of CNC MACHINING -
accusharp tooling #cnc #tooling #sigmayouthengineers
View: 1275Channel: CNC CAD CAM ACADEMY of SIGMA YOUTH ENGINEERS